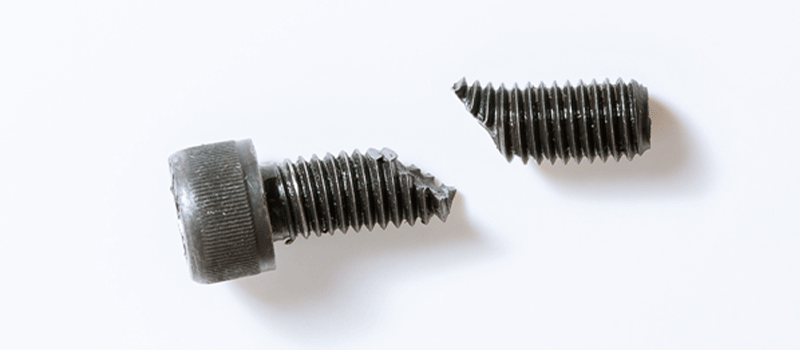
Bolt Failure: Causes and How to Prevent It
Bolts are mechanical fasteners that pair with nuts to connect two or more parts. Using them incorrectly can lead to serious problems. It is critical that you choose the correct nuts and bolts for the application and follow the manufacturer’s guidelines and best practices. Check out the video below to learn how bolts function, common causes of bolt failure, and tips to prevent bolt failure.
How do Bolts Work
Bolts are a crucial fastener for a wide range of applications including commercial and industrial products. The functionality of a bolt is pretty straightforward, but the mechanical properties and design are more complex.
Tightening a bolt generates several types of mechanical forces that help the joint remain secure. These forces include:
- Clamping Force – Compression that the bolt applies to the joint which holds the two components together.
- Preloading Force - Preload force keeps the threads in place once the bolt is turned. Preload force causes the threads to engage and stretch.
- Shear Force – Shear force is the pressure working against the bolt in a perpendicular direction.
- Tension Force – Tension force applies pressure to the length of the bolt in a vertical direction.
A bolt is inserted through parts that have unthreaded holes. A nut is then screwed onto the bolt creating a clamping force. This connection prevents axial movement. Bolts often rely on axial force. A specific amount of torque is applied to the head of the bolt to generate the axial force. To ensure it is properly tensioned during installation, we recommend using a torque wrench.
Bolt specifications are important to understand and keep in mind. This includes the type of bolt it is, its dimensions, thread density, material, grade, and tightening requirements. The type of nut that is used in conjunction with the bolt is also a critical factor in its overall performance.
- Check out our blog on understanding the markings and grades on nuts and bolts.
Causes of Bolt Failure
1. Bolt Fatigue Failure
Fatigue failure is the most common type of bolt failure. Fatigue failure can occur from several issues. These issues include:
- The bolt has not been sufficiently preloaded/tensioned during installation.
- The bolt lost its preload during service.
- The applied cyclic loading exceeded the strength of the bolt.
- The wrong grade of bolt was used for the application.
- The bolt had a quality issue.
Loosening of a bolt leads to fatigue failure. This is because the bolted joint can no longer absorb the external loads. The clamping force is then lost which prevents absorption into the parts and leads to increased load on the bolt. If a bolt experiences high levels of stress for a prolonged period of time, it is likely it will fail due to fatigue.
2. Shear Failure of a Bolt
Additionally, the shear failure of a bolt is a common type of bolt failure. Shear failure occurs when the shear stress exceeds the bolt’s shear strength. However, there are many factors that can cause shear failure to occur. It typically results in the joint members slipping sideways.
To avoid shear failure, it is recommended to do a thorough check on the connection. Avoid excessive overturning and tightening of the bolt during installation.
3. Bolt Thread Stripping
When tightening a bolt and the pairing of two threads occurs, shear stress gets added to the threaded part of the fastener. Thread stripping is a risk due to an excessive amount of stress.
To avoid joint failure from thread stripping, utilize a bolt with the correct thread design for the application.
4. Bolt Quality
The quality of a bolt plays a large role in preventing failure in the future. The quality can make a difference in its lifespan and strength. If you are using a bolt in a vital project, make sure the nuts and bolts are being replaced as soon as they are showing any signs of fatigue or loosening. We recommend investing in high-quality bolts from a reputable manufacturer. Fasteners Plus offers heavy-duty Conquest carriage bolts that are available in 304 stainless steel, 316 stainless steel, and hot dip galvanized options.
5. Bolt Corrosion
Bolts are commonly utilized in corrosive environments. They are at risk of rusting if they are exposed to incompatible substances including oxygen, metal products, and naturally-blending chemicals.
If a bolt is used in automobile components, they are in danger of being exposed to fluid and engine leaks. This can cause the fastener to deteriorate over time. Corrosion can occur in structural, construction, and mechanical applications.
6. Hydrogen Embrittlement
Hydrogen embrittlement is a failure that occurs from the retention or absorption of hydrogen in metal. The bolt's metal can become brittle after being exposed to atomic hydrogen. Overstressing the fastener can also cause hydrogen embrittlement.
Hydrogen damage can cause bolt failure in a short period of time. If your fastener is experiencing hydrogen damage, it is necessary that it is replaced right away.
To help prevent this failure from occurring, make sure the environment the bolts are exposed to is free of anodic chemicals and solvents that cause hydrogen embrittlement.
Tips to Prevent the Failure of Bolts
- Analyze the project the bolt will be used in. Understanding the application will help you determine the force the bolt will withstand.
- Assess the environment the bolt will be used in. If it will be used in an environment that experiences moisture, invest in corrosion-resistant nuts and bolts that will be able to withstand harsh environments.
- Invest in high-quality nuts and bolts that are the proper grade for the application.
- Make sure the bolts are not overstressed and the design is understood.
- Apply the correct torque value to tighten the bolt during installation.
- During installation, avoid misalignment, rough surfaces, and high-speed installation.
- Make sure the hole the bolt is fastened into is free from dirt and corrosion. A clear hole will ensure the torque reading is accurate.
- Utilize a bolt with the correct thread design for the application.